Understanding the hardness of carbide end mills is essential for those in the machining industry. Carbide end mills are known for their durability and efficiency, making them a popular choice among manufacturers and machinists. The hardness of these tools plays a significant role in their performance, wear resistance, and overall effectiveness during various machining operations.
Carbide is a composite material primarily made from tungsten carbide and cobalt. The unique properties of carbide give it superior hardness, resulting in tools that can withstand high temperatures and resist wear better than traditional steel tools. This is crucial when machining tough materials, as the end mills must maintain their cutting edge while working under extreme conditions.
One of the important aspects to consider is the grade of carbide used in the manufacturing of end mills. Higher-grade carbide will generally have a higher hardness rating, which translates to better performance. For example, many carbide end mills are rated using the Rockwell scale, with a rating of HRC 55 or higher indicating excellent hardness. This hardness allows for extended tool life and improved efficiency, leading to cost savings in the long run.
When selecting a carbide end mill, it's also essential to think about the coating that is applied to the tool. Coatings such as TiN (Titanium Nitride) or TiALN (Titanium Aluminum Nitride) can further enhance the hardness and performance of carbide end mills. These coatings provide additional wear resistance and help reduce friction during cutting, allowing for smoother operations and better surface finishes.
Moreover, understanding how the hardness of carbide end mills affects the actual machining process is vital. Tools with higher hardness ratings can handle tougher materials and maintain sharp edges over longer periods. Consequently, this leads to fewer tool changes and less downtime, which is critical for maximizing productivity on the shop floor.
For those looking to upgrade their tooling, a reliable source for high-quality carbide end mills is crucial. Companies like
Ruihan Tools offer a range of options to suit various machining needs. Their commitment to quality ensures that you receive tools that not only meet but exceed industry standards in hardness and performance.
Furthermore, as industries continue to advance and demand increases for quicker and more efficient machining, the significance of understanding the
hardness of carbide end mills cannot be overstated. Making informed choices about tooling directly affects productivity, cost, and the quality of finished products.
In conclusion, the hardness of carbide end mills is a crucial factor that influences manufacturing processes. By selecting the right grade of carbide and considering tool coatings, manufacturers can improve efficiency and reduce costs. Investing in quality carbide end mills from trusted suppliers like
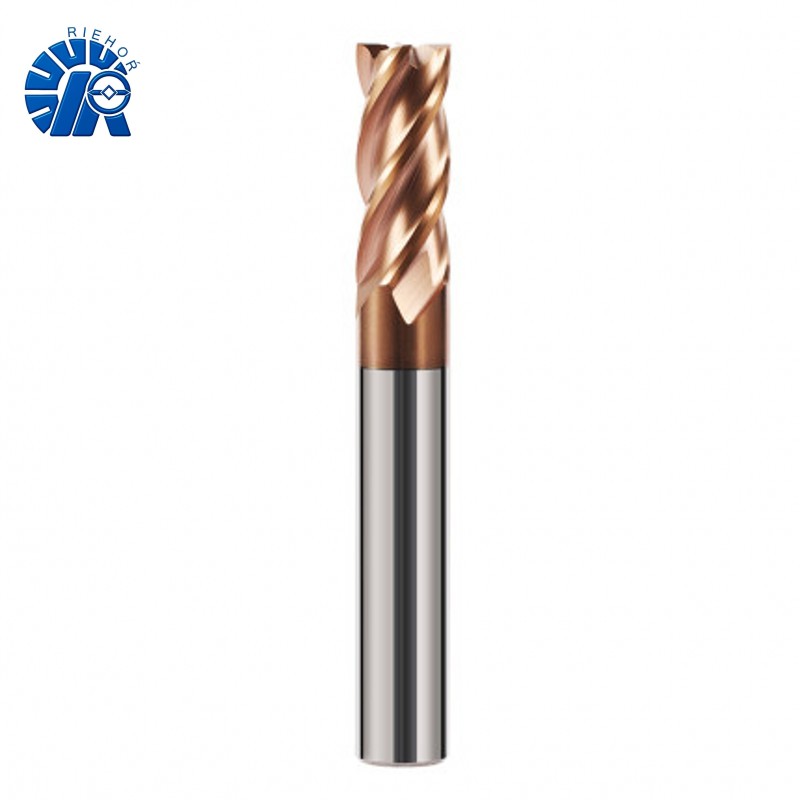
and understanding their specifications can lead to significant improvements in production and quality outcomes. Whether you are a seasoned machinist or a newcomer to the field, grasping the significance of carbide end mill hardness will undoubtedly enhance your machining capabilities.
Comments
All Comments ( 0 )